painting coating filter
Introduction Providing a cost-effective fi ltration technology that ensures consistent quality and process optimization
Parker domnick hunter’s proven product range and applications experience in the inks, paints, and specialty coatings industry enables us to ensure that every step of the manufacturing process meets the customers' quality specifi cations. The manufacture and application of an ink or coating can be divided into the following processes:
• Resin processing and introduction of resins to blending and dispersion phases.
• Production of deionized water for use in aqueous based product.
• Additives and raw materials for the dispersion phase.
• Product manufacturing processes where the pigments are milled and blended with either solvent or water and packaged.
• Packaging and transportation of the liquid products to the application, whether it is printed, painted, or coated.
Given the variations of these processes for inks, paints, or specialty coatings, it is critical to consider the operating parameters when selecting fi ltration for each stage of manufacturing.
As formulations become more complex, the manufacturing process demands also become increasingly more critical. With increasing energy and disposal costs, it is important that the recommended fi ltration systems provide minimal process downtime and low product waste, so the total cost of ownership of the fi ltration system is balanced, without compromising the quality of the end product.
MARKET APPLICATIONS Additives & Raw Materials
• Diluents • Fillers • Primers • Stabilizers • Surfactants • Resins • Polymers • Water • Pigment • Oils • Plasticizers • Emulsions • Solvents
Commerical & Industrial Coatings • Adhesives • Aerosols • Architectural paint • Caulks • Corrosion inhibitors • Dyes • Finishes • Marine coatings • Packaging coatings • Primers • Sealants • Shellac • Varnishes • Lacquer • Wood fi nishes
Printing Inks • Can coatings • Conductive • Film coatings • Flexographic • Gravure • Heat set inks • Ink jet printing • Lithographic • Non-impact • Screen printing • UV sensitive
Specialty & Performance Coatings • Automotive • Clear coats • Flooring systems • Fluorescent coatings • Glaze • High performance coatings • Optical coatings • Protective coatings • Road paints • Stains • Textured fi nishes • Transparent armors • Water proofi ng
Resins such as acrylics, alkyds, epoxies and polyesters are key constituents of paints and inks and with the development of more sophisticated coatings, resin quality specifi cations are becoming more stringent.
The variable process conditions during resin manufacturing can result in a variety of contaminants such as: • Haze • Salts • Deformable gels • Fibers • Semi-solid particles
These affect the fi nal fi nish of the coating by causing defects such as “fi sh-eyes”, cratering and lead to poor fi nishes.
Incorrect fi lters can lead to: • Re-working (re-classifi cation) of the resin • Resin waste • Excessive fi lter replacements
Resulting increase in: • Disposable costs • Energy costs • Recirculation of batches
Leading to overall higher manufacturing costs.
The varying size distribution of the contaminants offer a challenge that requires multiple fi lter types and stages.
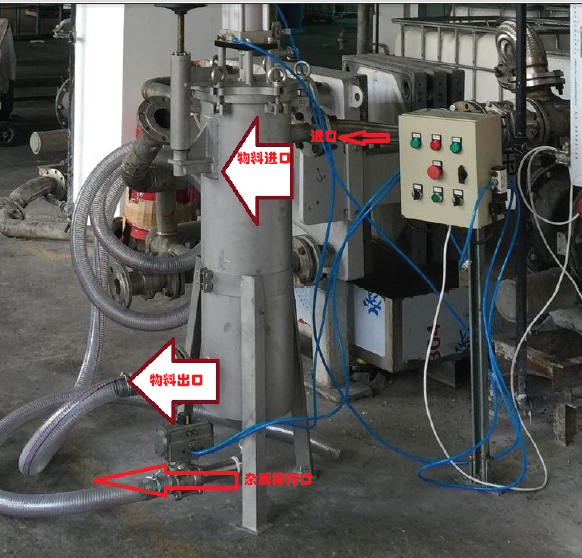