Tubular Backwash Filters

Tubular Backwash Filter Systems are designed for continuous operation with high flow rates in applications with low solids loadings. These systems can operate in 2 different Backwash Modes depending upon your process requirements.
Tubular Filter Series is a family of tubular type, in-line pressure filters used for the separation of suspended solids from a liquid stream. The basic building block is the tubular filter which consists of two parts: the outer housing and a removable reusable filter element. TF Tubular Filters provide the flexibility to accommodate a wide variety of process filtration requirements.
Configurations range from single tube, manually cleaned filters to multiple tubes connected to common manifolds for inlet, outlet, backwash and drain. Custom designs are available to meet your space, piping, or process requirements. Multiple tube TF Filter Systems may be provided as a complete factory assembled package with PLC controlled operation of actuated valves to control backwashing of the system based on differential pressure or time. Durco Filters TF Filters are available with wetted parts
Sample Applications: Pulp & Paper Mills White Water
River Water Spray Nozzle Protection
Petrochemicals Brine
Caustic Hydrochloric
Food and Beverage Fruit Juices
Vegetable Oils Syrups Pharmaceutical and Cosmetics Acetic Acid Bath
Oil Citric Acid Glycerin Guard Filters
Pre-Filtration Boiler
Feed Water Condensate
Internal backwash utilizes the system’s filtrate to clean the system. This is accomplished by changing the lower valve from the inlet to the drain position on one filter unit. A portion of the filtrate from the remaining on-stream units flows in the reverse direction through the backwashing unit to dislodge collected solids. Each unit is backwashed in turn, individually and consecutively to return the system to a clean condition. Internal backwash should be considered when the process stream is of sufficient flow and pressure to ensure an adequate backwash, or when the process stream is
External backwash uses a clean secondary liquid stream, typically plant water, supplied by an additional header to clean the system. This is accomplished by rotating the upper valve to the backwash position and the lower valve to the drain position. The backwashing filter unit is cleaned by the reverse flow of the external stream. Each unit is backwashed in turn, individually and consecutively to return the system to a clean condition. During backwashing, a continuous uninterrupted process flow can be maintained by the remaining on-stream units. External backwash should be considered when the process stream is not of sufficient flow and pressure to ensure an adequate backwash, or when the process stream is valuable or creates a disposal problem
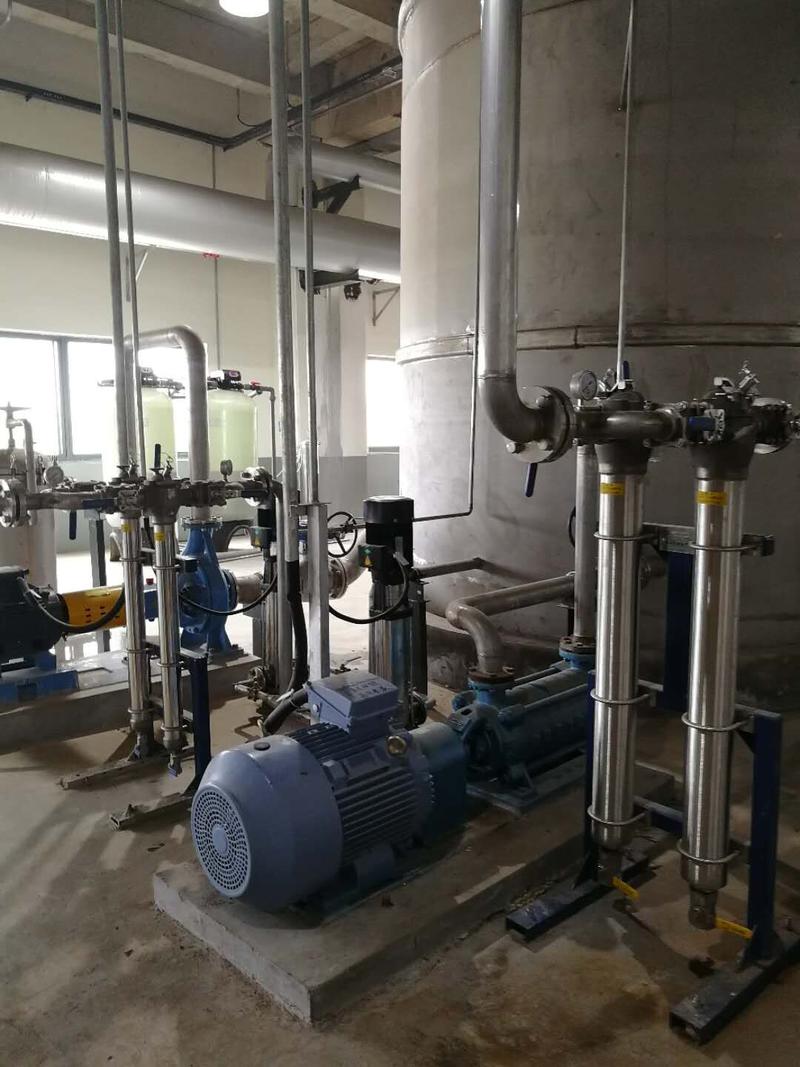
The basic objective in solid/liquid separation is efficient particulate removal. There are a number of methods of achieving this, one method being the tubular filter.
The ability of a specific liquid containing suspended solids to filter through a septum for the removal of solids is called filterability. Factors which affect filterability include: pressure, temperature, cake compressibility, specific case resistance, and fluid viscosity.
Regardless of shape, a tube filter is a series of enclosed tubes containing a filter septum or element. Either slotted or perforated elements can be used in a multitude of mesh sizes depending on the particulate size needing to be filtered.
Due to the variety of applications, laboratory and/or “on-site” pilot testing are advisable. We have many pilot filters and a complete laboratory to thoroughly analyze process fluids and test for filterability.
particulate removal. There are a number of methods of achieving this, one method being the tubular filter.
The ability of a specific liquid containing suspended solids to filter through a septum for the removal of solids is called filterability. Factors which affect filterability include: pressure, temperature, cake compressibility, specific case resistance, and fluid viscosity.
Regardless of shape, a tube filter is a series of enclosed tubes containing a filter septum or element. Either slotted or perforated elements can be used in a multitude of mesh sizes depending on the particulate size needing to be filtered.
Due to the variety of applications, laboratory and/or “on-site” pilot testing are advisable. We have many pilot filters and a complete laboratory to thoroughly analyze process fluids and test for filterability.
We can equip any Filters unit with an automated system to suit your needs. From semi-automatic, where sequence steps are activated by the operator, to fully-automatic with a central control panel, or even DCS controlled, we can equip your system with the control scheme that fits your operational requirements. If desired, these systems can be equipped with the ability to monitor process conditions such as flow rate, turbidity, etc.
Completely piped, wired, and skid mounted systems are available to ensure minimum installation time. We provide installation supervision, start-up services, and instructions to plant operators in the functioning and maintenance of the system, in all languages worldwide